Mechanical Properties
Among the various plastic films available, Lumirror™ features high tensile strength and is so tough that it cannot be ripped by hand, even with a thickness of 0.025 mm. Using thin materials, products can be made smaller, lighter, or be given higher performance.
1. Tensile Strength and Elongation for Various Product Numbers
Table 1 shoes the tensile strength and elongation for various Lumirror™ product numbers.
The measurement method is JIS C 2318-72.
Thickness | MD (Vertical) | TD (Horizontal) | |||
---|---|---|---|---|---|
Tensile Strength | Tensile Elongation | Tensile Strength | Tensile Elongation | ||
Product No. | μ | kg/mm2 | % | kg/mm2 | % |
#6 | 6 | 20.0 | 130 | 24.0 | 90 |
#9 | 9 | 20.0 | 130 | 27.0 | 100 |
#12 | 12 | 22.0 | 140 | 26.0 | 120 |
#16 | 16 | 22.0 | 150 | 25.0 | 120 |
#25 | 25 | 21.0 | 160 | 25.0 | 130 |
#38 | 38 | 23.0 | 140 | 25.0 | 130 |
#50 | 50 | 22.0 | 150 | 22.0 | 130 |
#75 | 75 | 22.0 | 150 | 22.0 | 130 |
#100 | 100 | 21.5 | 150 | 21.0 | 130 |
#125 | 125 | 21.0 | 150 | 20.0 | 140 |
#188 | 188 | 19.0 | 190 | 19.0 | 140 |
#250 | 250 | 18.0 | 190 | 17.5 | 150 |
#350 | 350 | 16.0 | 190 | 15.0 | 160 |
2. Comparison of Tensile Strength and Elongation with Other Films
Among the various plastic films available, Lumirror™ has the highest tensile strength. Table 2 shows the tensile strength and elongation of various plastic films measured under the same conditions for the purpose of comparison.
The thickness of each sample measured was 25 μ, and the test conditions were 20°C and 65% RH.
Film | Tensile Strength | Tensile Elongation |
---|---|---|
kg/mm2 | % | |
Lumirror™ | 24 | 130 |
TORAYFAN™ NO *1 | 3 to 5 | 700 |
TORAYFAN™ BO *2 | 19 | 130 |
High pressure polyethylene | 2 | 300 |
Stretched polystyrene | 10 | 10 to 20 |
Nylon 6 | 10 | 400 |
Stretched nylon 6 | 10 to 25 | 50 to 130 |
Stretched polycarbonate | 10 | 150 |
Soft polyvinyl chloride | 3 to 4 | 300 |
Hard polyvinyl chloride | 5 | 30 to 130 |
Stretched hard polyvinyl chloride | 12 | 80 |
Stretched vinyl chloride, vinylidene chloride copolymer | 12 | 70 |
Hydrochloric acid rubber | 10 | 130 |
Cellulose triacetate | 12.5 | 40 |
Cellophane | 12 to 20 | 15 |
- 1 Toray unstretched polypropylene film
- 2 Toray biaxially oriented polypropylene film
3. Changes in Tensile Strength and Elongation Due to Temperature
Changes in Lumirror™ tensile strength and elongation based on temperature are shown in Figures 1 and 2.
The thickness of each sample measured was #38 (38 μ) and the measurement method was JIS C 2318-72.
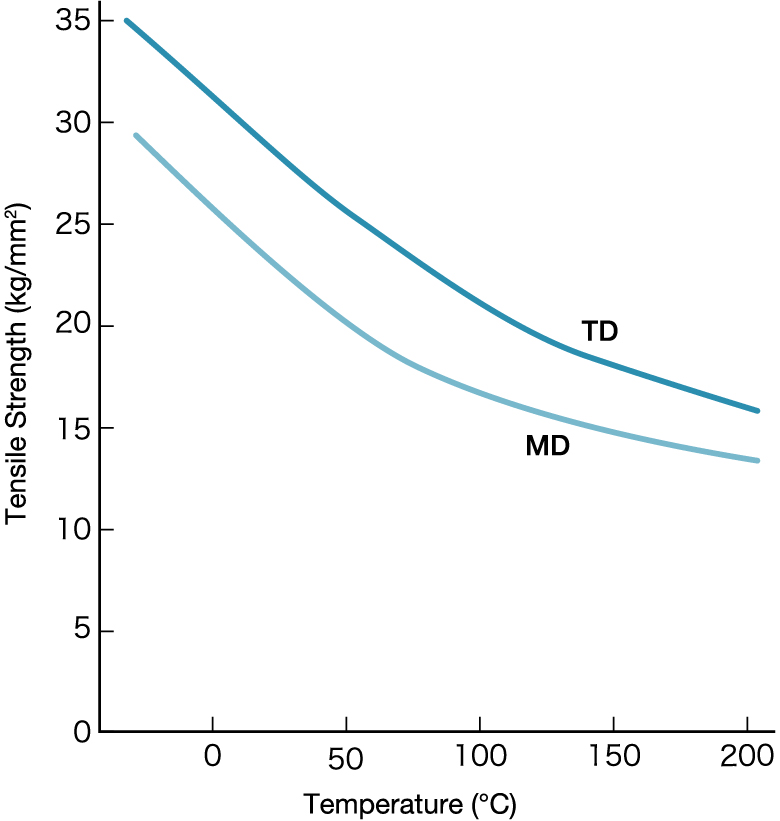
Based on Temperature
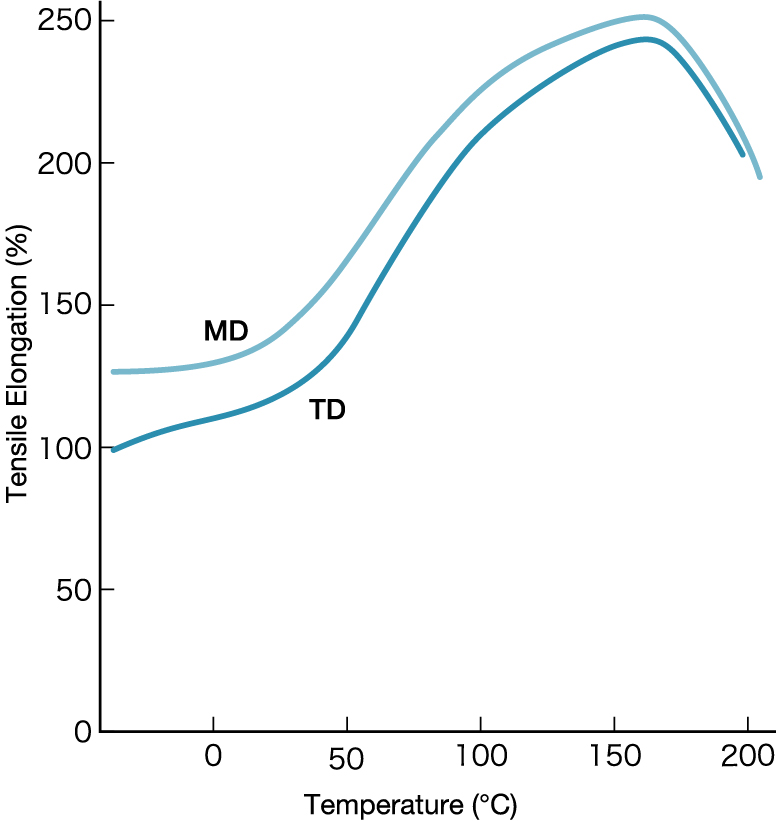
Based on Temperature
4. Change in Tensile Strength and Elongation Curve Based on Temperature
Lumirror™ retains excellent mechanical characteristics throughout a wide temperature range of -70 to +150°C.
Fig. 3 shows the tensile strength and elongation curve for #38 (38 μ) Lumirror™ measured between the temperatures of -20 and +200°C.
The measurement method is JIS C 2318-72.
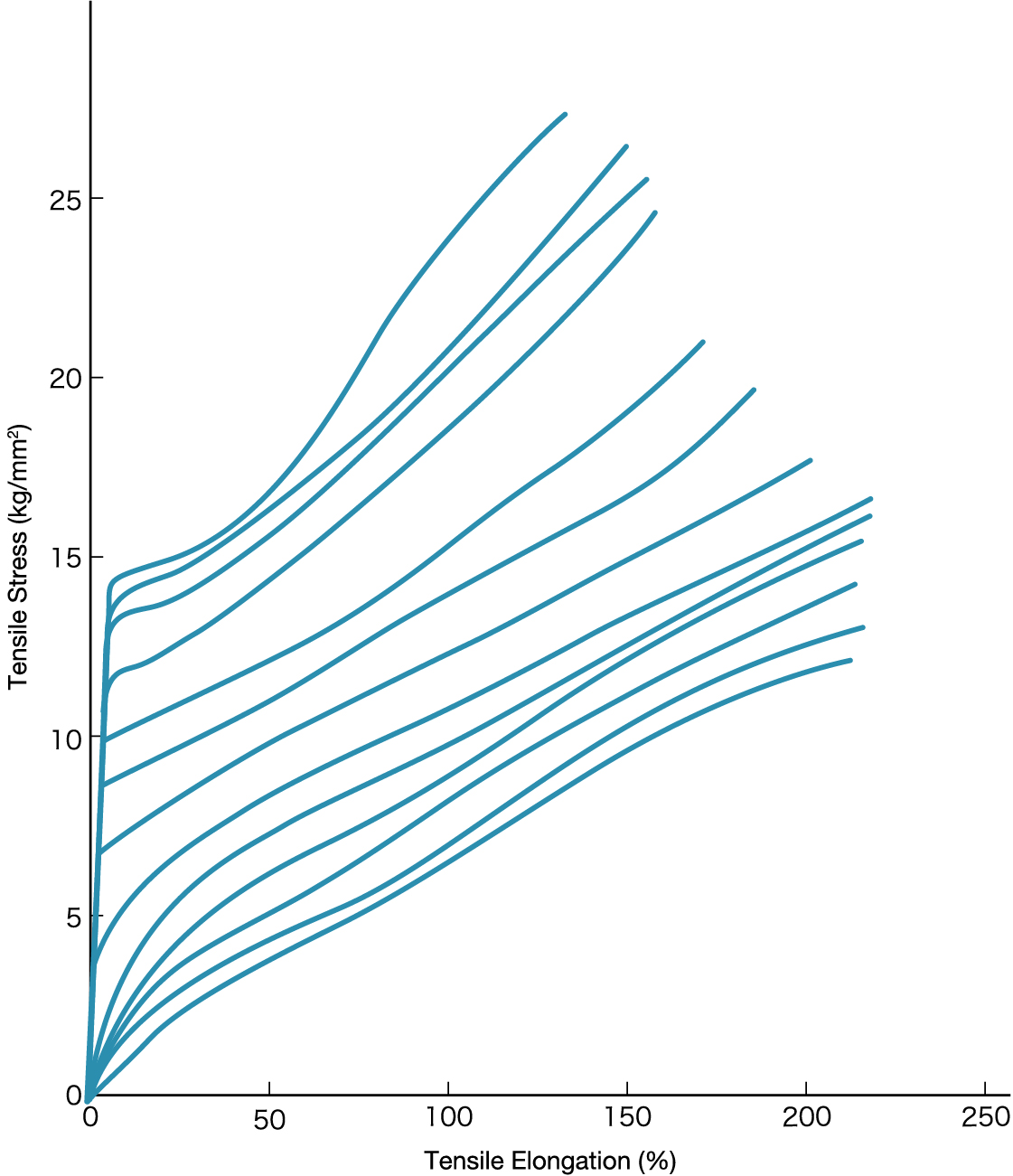
5. Comparison of Tensile Modulus with Other Films
Among the various plastic films available, Lumirror™ has the largest tensile modulus.
Table 3 shows the tensile modulus of various plastic films measured under the same conditions for the purpose of comparison.
The thickness of each sample measured was 25 μ, and the test conditions were 20°C and 65% RH.
Film | Tensile Modulus |
---|---|
kg/mm2 | |
Lumirror™ | 400 |
TORAYFAN™ NO *1 | 90 |
TORAYFAN™ BO *2 | 200 |
High pressure polyethylene | 20 |
Stretched polystyrene | 120 |
Nylon 6 | 60 |
Stretched nylon 6 | 150 |
Stretched polycarbonate | 110 |
Soft polycarbonate | 20 |
Hard polyvinyl chloride | 140 |
Stretched hard polyvinyl chloride | 300 |
Stretched vinyl chloride, vinylidene chloride copolymer | 40 |
Hydrochloric acid rubber | 140 |
Cellulose triacetate | 300 |
Cellophane | 150 to 320 |
- 1 Toray unstretched polypropylene film
- 2 Toray biaxially oriented polypropylene film
6. Changes in Tensile Stress When Slightly Elongated Based on Temperature
Lumirror™'s tensile stress when it is elongated by just a small amount does not increase or change rapidly, as Lumirror™ normally has excellent cold resistance even at temperatures lower than room temperature.
However, one characteristic of thermoplastic resins is that they gradually weaken at temperatures higher than room temperature.
Fig. 4 shows the changes in #75 (75 μ) Lumirror™ tensile stress when elongated by 1%, 3%, and 5% based on temperature.
The measurement method is JIS C 2318-72.
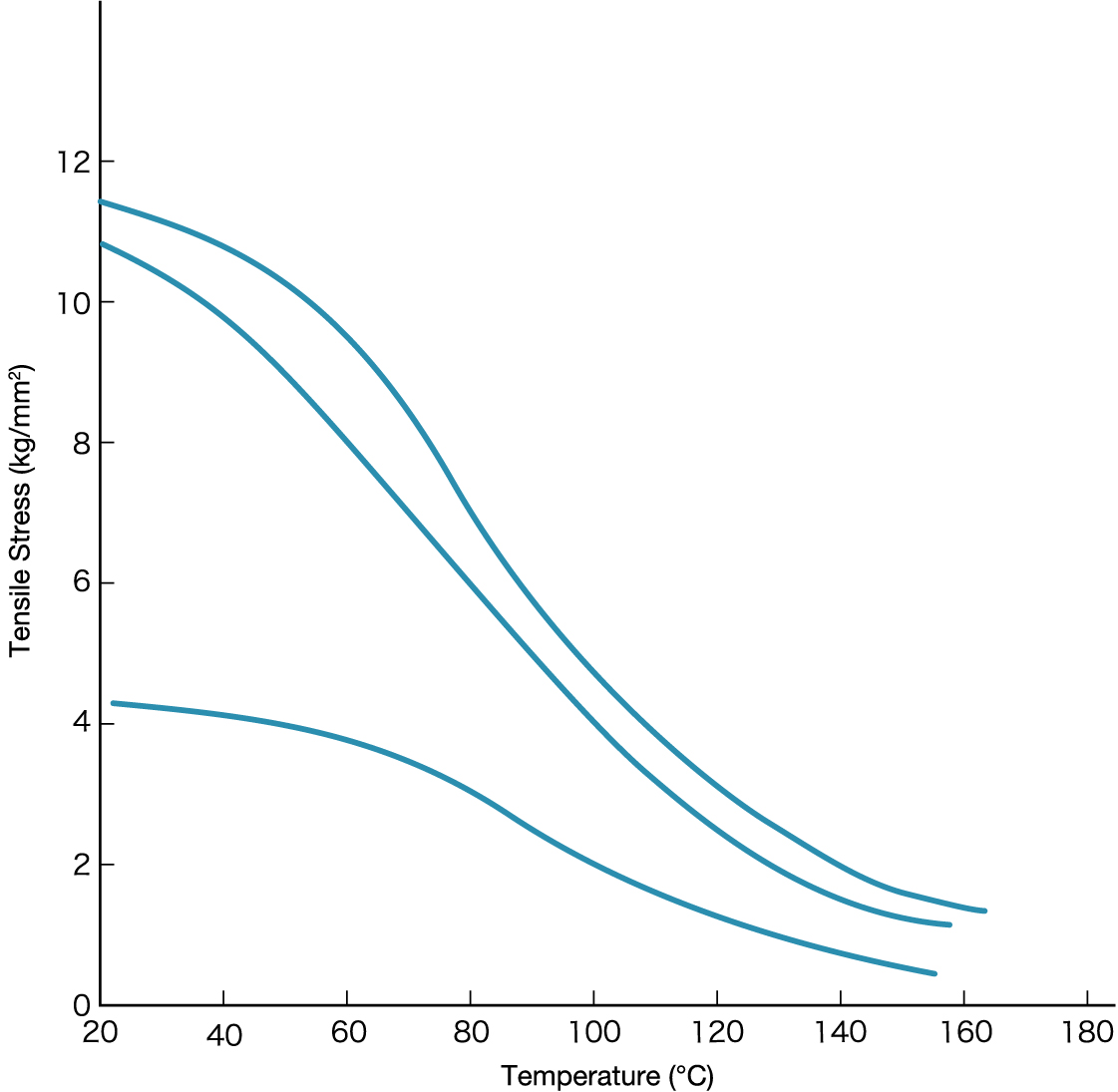
7. Changes in Dynamic Characteristics Based on Temperature
Fig. 5 shows the dynamic tensile modulus and tan δ for #12 (12 μ) Lumirror™.
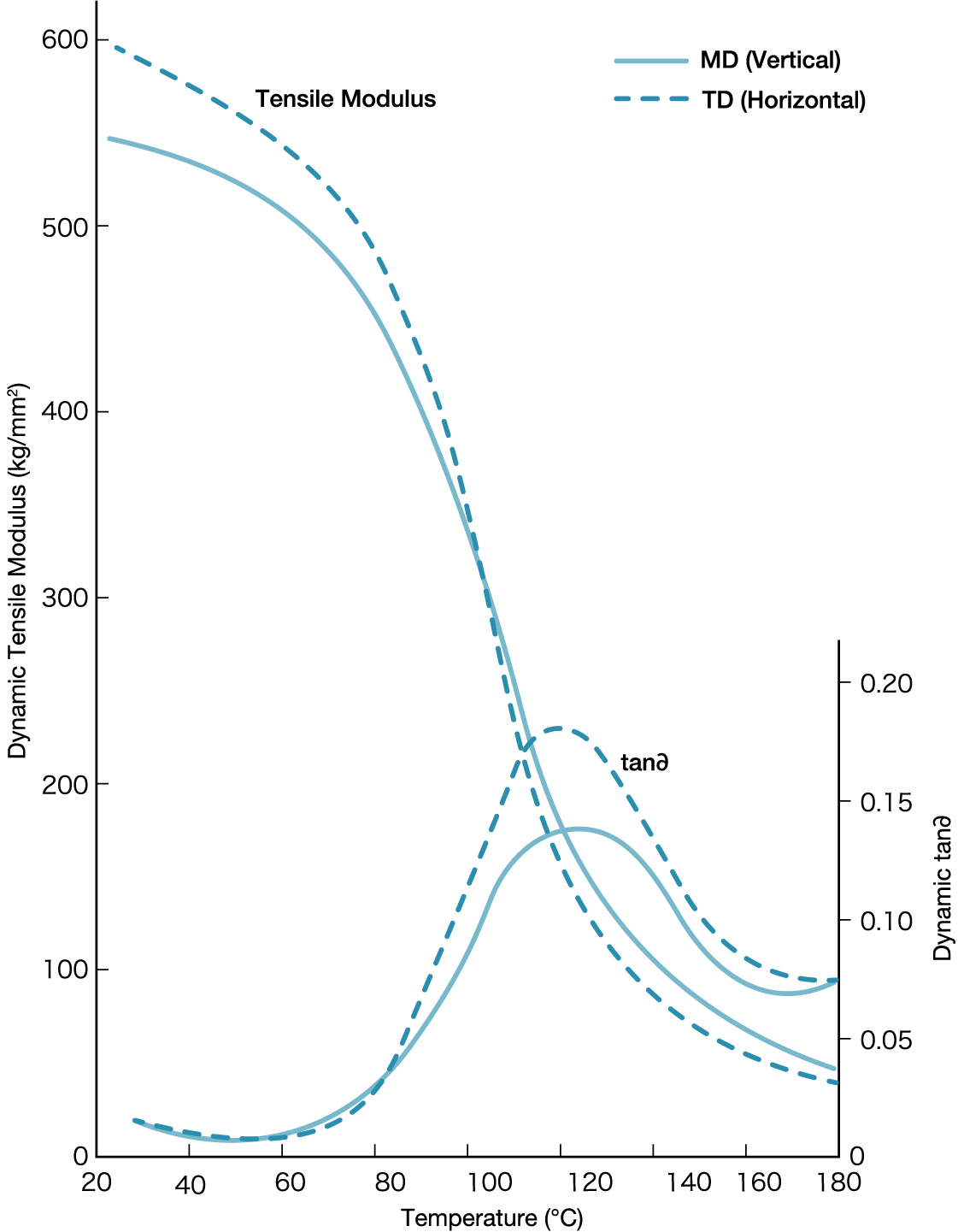
8. Creep Characteristics
Fig. 6 shows the creep characteristics for #188 (188 μ) Lumirror™ measured at a tension of 2 to 10 kg/mm2. The width of the measured samples was 10 mm, the length was 1,000 mm, and the test conditions were 25°C and 65% RH.
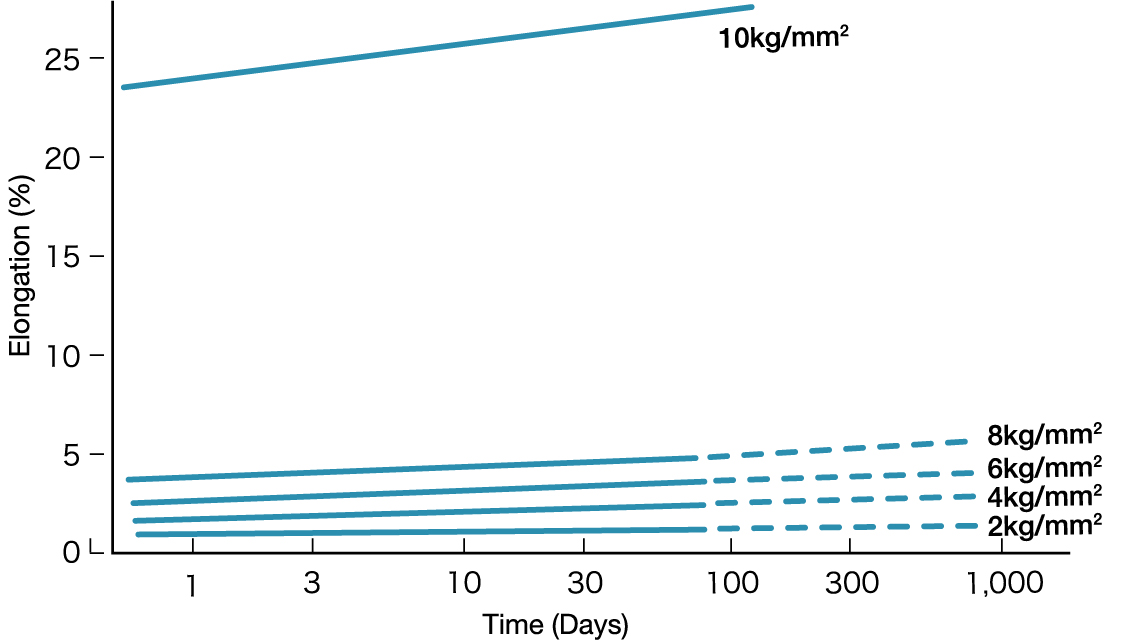
9. End Tear Resistance for Various Product Numbers
Table 4 shows the end tear resistance for various Lumirror™ product numbers.
The measurement method is JIS C 2318-72.
Height | MD (Vertical) | TD (Horizontal) | |
---|---|---|---|
Product No. | μ | kg/20mm | kg/20mm |
#6 | 6 | 4.8 | 3.6 |
#9 | 9 | 7.0 | 6.0 |
#12 | 12 | 9.0 | 9.0 |
#16 | 16 | 14.5 | 13.0 |
#25 | 25 | 22.0 | 20.0 |
#38 | 38 | 32.0 | 30.0 |
#50 | 50 | 40.0 | 36.5 |
#75 | 75 | 60.0 | 56.5 |
#100 | 100 | 72.0 | 73.0 |
#125 | 125 | 87.5 | 88.0 |
#188 | 188 | 125.0 | 130.0 |
#250 | 250 | 150.0 | 160.0 |
#350 | 350 | 200.0 | 240.0 |
10. Comparison of End Tear Resistance with Other Films
Among the various plastic films available, Lumirror™ has the highest end tear resistance. Table 2 shows the end tear resistance of various plastic films for the purpose of comparison. Values are all obtained with a thickness of 25 μ and the measurement method is JIS C 2318-72.
Film | End Tear Resistance |
---|---|
kg/20mm | |
Lumirror™ | 22 |
TORAYFAN™ NO *1 | 3 |
TORAYFAN™ BO *2 | 15 |
High pressure polyethylene | 2 |
Stretched polystyrene | 0.3 to 1.5 |
Nylon 6 | 5 |
Stretched nylon 6 | 20 |
Soft polyvinyl chloride | 3 |
Hard polyvinyl chloride | 6 |
Stretched hard polyvinyl chloride | 10 |
Stretched vinyl chloride, vinylidene chloride copolymer | 10 |
Hydrochloric acid rubber | 10 |
Cellulose triacetate | 4 |
Cellophane | 6 |
Moisture-proof cellophane | 4 |
Polyethylene laminate cellophane | 5 |
- 1 Toray unstretched polypropylene film
- 2 Toray biaxially oriented polypropylene film
11. Rupture Strength for Various Product Numbers
Table 6 shows the rupture strength for various Lumirror™ product numbers.
The measurement method is JIS P8112-63.
Thickness | Rupture Strength | ||
---|---|---|---|
Product No. | μ | kg/cm2 | kg/cm2/mm |
#6 | 6 | 1.53 | 255 |
#16 | 16 | 4.89 | 305 |
#25 | 25 | 6.00 | 240 |
#38 | 38 | 9.19 | 242 |
12. Comparison of Rupture Strength with Other Films
Among the various plastic films available, Lumirror™ has the highest rupture strength.
Table 7 shows the rupture strength of various plastic films for the purpose of comparison.
Film | Rupture Strength |
---|---|
kg/cm2/mm | |
Lumirror™ | 200 to 300 |
TORAYFAN™ BO *1 | 150 to 170 |
High pressure polyethylene | 6 to 10 |
Soft polyvinyl chloride | 40 to 60 |
Stretched vinyl chloride, vinylidene chloride copolymer | 60 to 70 |
Cellophane | 80 to 100 |
Moisture-proof cellophane | 60 to 70 |
- 1 Toray biaxially oriented polypropylene film
13. Comparison of Impact Strength with Other Films
Among the various plastic films available, Lumirror™ has the highest impact strength.
Table 8 shows the impact strength of various plastic films for the purpose of comparison. The thickness of each measured sample was 25 μ, and the measurement method was the JIS K6745-72 falling ball method at 25°C.
Film | Impact Strength (25 μ) | |
---|---|---|
kg・cm | kg・cm/mm | |
Lumirror™ | 25 | 1,000 |
TORAYFAN™ NO *1 | 1 | 40 |
TORAYFAN™ BO *2 | 17 | 680 |
High pressure polyethylene | 4 | 160 |
Stretched polystyrene | 0.6 | 24 |
Nylon 6 | 12 | 480 |
Stretched nylon 6 | 25 | 1,000 |
Stretched polycarbonate | 25 | 1,000 |
Soft polyvinyl chloride | > 9 | > 360 |
Hard polyvinyl chloride | 2 | 80 |
Stretched hard polyvinyl chloride | 18 | 720 |
Stretched vinyl chloride, vinylidene chloride copolymer | 10 | 400 |
Hydrochloric acid rubber | > 15 | > 600 |
Cellulose triacetate | 8 | 320 |
Cellophane | 9 | 375 |
Moisture-proof cellophane | 9 | 360 |
Polyethylene laminate cellophane | 7 | 280 |
- 1 Toray unstretched polypropylene film
- 2 Toray biaxially oriented polypropylene film
14. Tear Propagation Resistance for Various Product Numbers
Table 9 shows the tear propagation resistance for various Lumirror™ product numbers.
The measurement method is JIS P8116-73.
Thickness | MD (Vertical) | TD (Horizontal) | |
---|---|---|---|
Product No. | μ | g | g |
#12 | 12 | 10 | 8 |
#25 | 25 | 20 | 15 |
#38 | 38 | 27 | 25 |
#50 | 50 | 35 | 30 |
#75 | 75 | 52 | 45 |
#100 | 100 | 79 | 77 |
#125 | 125 | 90 | 94 |
#188 | 188 | 140 | 146 |
#250 | 250 | 187 | 180 |
#350 | 350 | 313 | 316 |
15. Folding Endurance
Table 10 shows the folding endurance of Lumirror™ (number of times it can be folded).
The measurement method was JIS P8115-63 with the test performed at room temperature.
Thickness | MD (Vertical) | TD (Horizontal) | |
---|---|---|---|
Product No. | μ | Tension 250 kg/cm2 | Tension 100 kg/cm2 |
#12 | 12 | > 120,000 | > 120,000 |
#25 | 25 | > 120,000 | > 120,000 |
#50 | 50 | 38,600 | 85,200 |
#125 | 125 | 25,800 | 38,300 |
#250 | 250 | 4,000 | 22,000 |
16. Bending Recovery Rate
The bending recovery rate of Lumirror™ was measured as follows.
A 10 mm wide × 60 mm long sample had a 275 g weight with a base of 30 mm × 40 mm placed on a spot 20 mm from the edge where the film was bent 180°. After one minute, the weight was removed and the recovery amount immediately after removal, as well as the recovery amount after one minute was measured.
The results of these measurements are shown in Table 11.
Thickness | Instant Recovery Rate | Recovery Rate After 1 Minute | |
---|---|---|---|
Product No. | μ | % | % |
#12 | 12 | 18 | 32 |
#25 | 25 | 25 | 69 |
#250 | 250 | 75 | 83 |
17. Friction Coefficient
Table 12 shows the friction coefficient of Lumirror™.
The measurement method is ASTM D 1894-63.
Height | Static Friction Coefficient | Dynamic Friction Coefficient | |
---|---|---|---|
Product No. | μ | ||
#25 | 25 | 0.44 | 0.40 |
#50 | 50 | 0.43 | 0.35 |
#125 | 125 | 0.25 | 0.21 |