Physical and Thermal Properties
1. General Physical Properties
Table 1 summarizes the physical properties of Lumirror™.
The thickness of each sample used for measurement was #25 (25 μ).
Property | Measurement Value | Unit | Measurement Method |
---|---|---|---|
Density | 1.40 (1.390 to 1.408) |
g/cm2 | JIS K 6760 - 71 (n–Heptane, CCI4) |
Melting Point | 263 | °C | With heating stage Observed using a microscope |
Specific Heat | 0.32 | cal/g/°C | |
Heat Transfer Coefficient | 3.36 × 10-4 | cal/cm/sec/°C | |
Moisture Expansion Coefficient | 1.2 × 10-5 | cm/cm/%RH | |
Thermal Expansion Coefficient | 1.5 × 10-5 | cm/cm/°C | ASTM D 696- 70 |
Refractive Index | 1.66 | ASTM D 542 - 70 (Abbe, 20°C) |
|
Light Transmittance | 85 | % | JIS K 6714 - 58 |
2. Change in Hygroscopic Rate Based on Relative Humidity
Fig. 1 shows the changes in the hygroscopic rate as the amount of humidity Lumirror™ is exposed to increases.
Measurements were taken at 25°C.
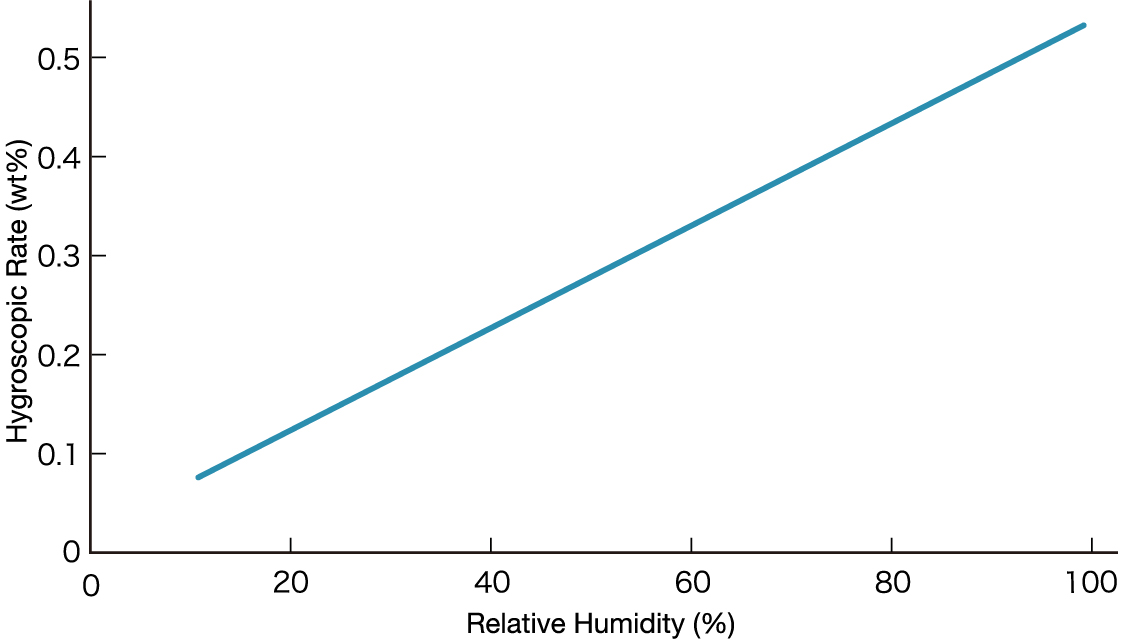
3. Water Absorption Rate for Various Product Numbers
Fig. 2 shows the water absorption rate of various Lumirror™ product numbers when immersed in 20°C water for 24 hours and when immersed in 100°C boiling water for 2 hours.
The measurement method is the Federal Test Method Std. NO. 406 Method 7031.
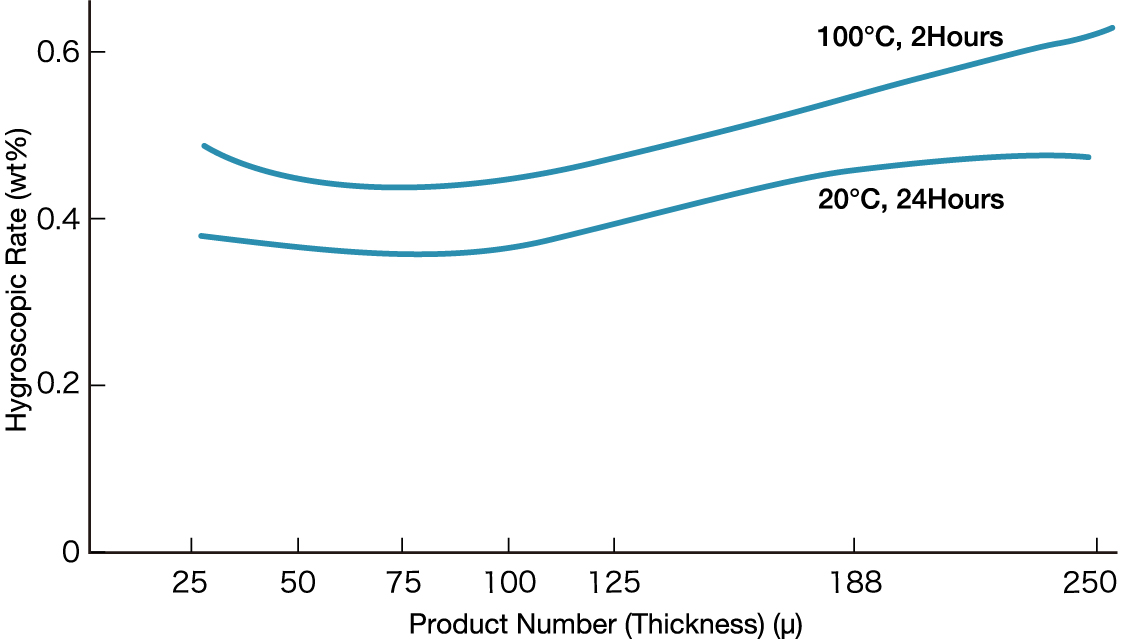
4. Drying Curve
Lumirror™ was dried at 120°C until it reached a state of equilibrium, and then it was allowed to achieve sufficient equilibrium at room temperature in either 80% RH or normal humidity. After, the change in weight and the change over time were measured and recorded for both #75 (75 μ) and #188 (188 μ) as the samples were once again dried at 120°C. The results of these measurements are shown in Fig. 3.
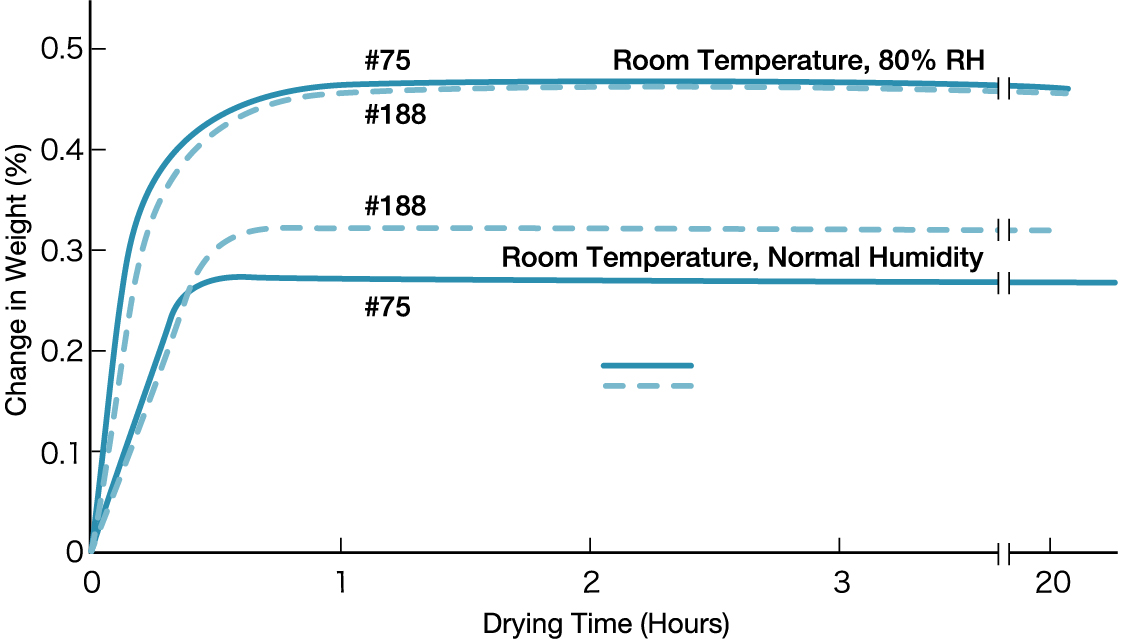
5. Moisture-related Dimensional Stability
Fig. 4 shows the dimensional change of Lumirror™ as it is exposed to increasing humidity.
The moisture expansion coefficient of Lumirror™ is calculated from Fig. 4 as follows.
1.2 × 10-5 cm / cm / %RH
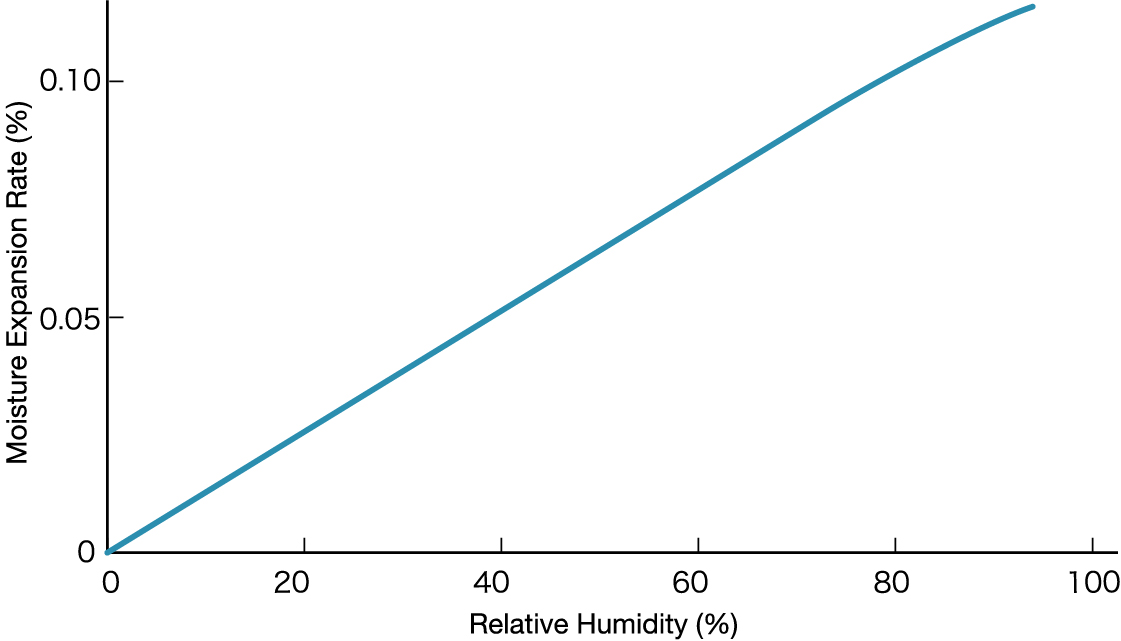
6. Thermal Dimensional Stability
Fig. 5 shows the dimensional change of Lumirror™ #50 (50 μ) as it is exposed to temperatures from room temperature up to around 100°C.
The thermal expansion coefficients of Lumirror™ around room temperature are as follows.
The measurement method is ASTM D 696-70.
MD (Vertical): 1.2 × 10-5 cm / cm / °C
TD (Horizontal): 1.6 × 10-5 cm / cm / °C
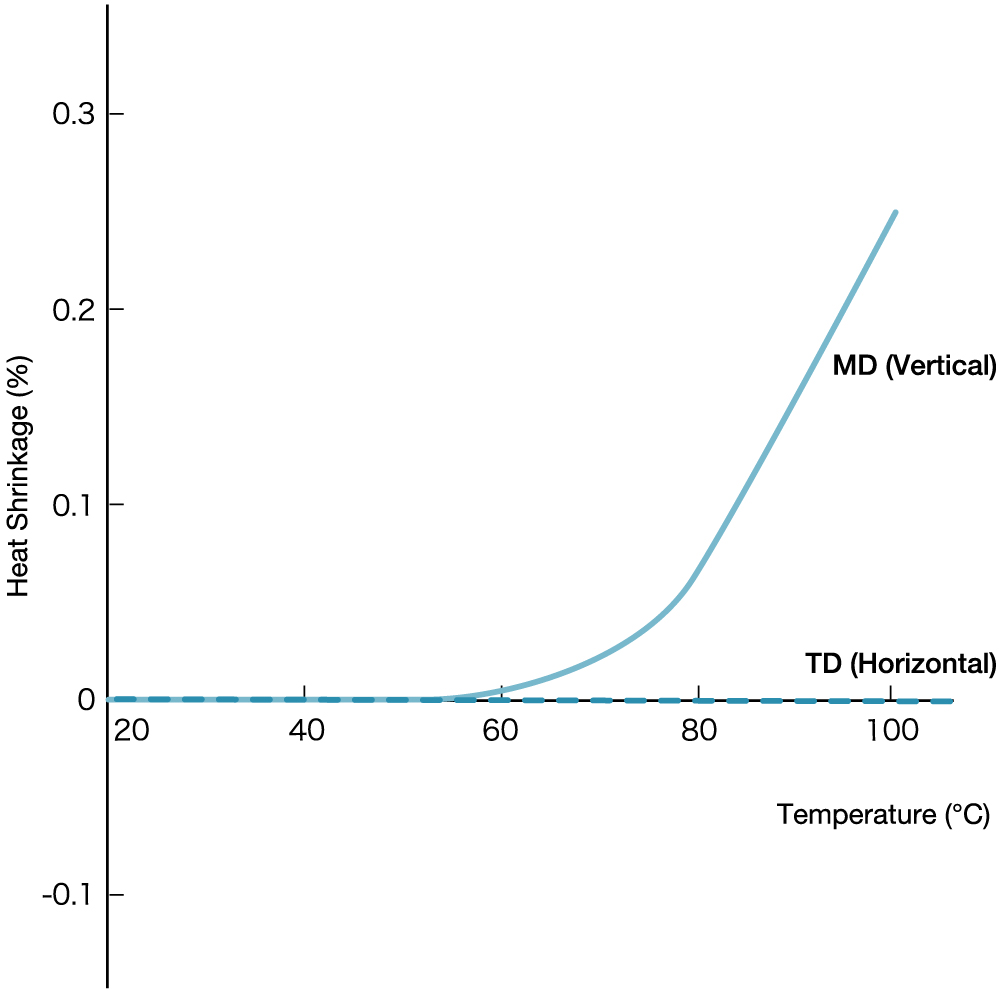
7. Heat Shrinkage for Various Product Numbers
Table 2 shows the heat shrinkage for various Lumirror™ product numbers at 150°C for 2 hours.
The measurement method uses a reading microscope in accordance with JIS C 2318-72.
Thickness | MD (Vertical) | TD (Horizontal) | |
---|---|---|---|
Product No. | μ | % | % |
#6 | 6 | 1.6 | 1.2 |
#9 | 9 | 1.5 | 1.2 |
#12 | 12 | 1.3 | 0.2 |
#16 | 16 | 1.5 | 0.5 |
#25 | 25 | 1.3 | 1.0 |
#38 | 38 | 1.3 | 0.4 |
#50 | 50 | 1.2 | 0.2 |
#75 | 75 | 1.2 | 0.3 |
#100 | 100 | 1.2 | 0.3 |
#125 | 125 | 1.2 | 0.7 |
#188 | 188 | 1.3 | 0.7 |
#250 | 250 | 1.2 | 0.7 |
#350 | 350 | 1.2 | 0.7 |
8. Changes in Heat Shrinkage Rate Based on Temperature
Fig. 6 shows the heat shrinkage rate of #50 (50 μ) Lumirror™ at temperatures from 90 to 190°C.
The measurement method is JIS C 2318-72.
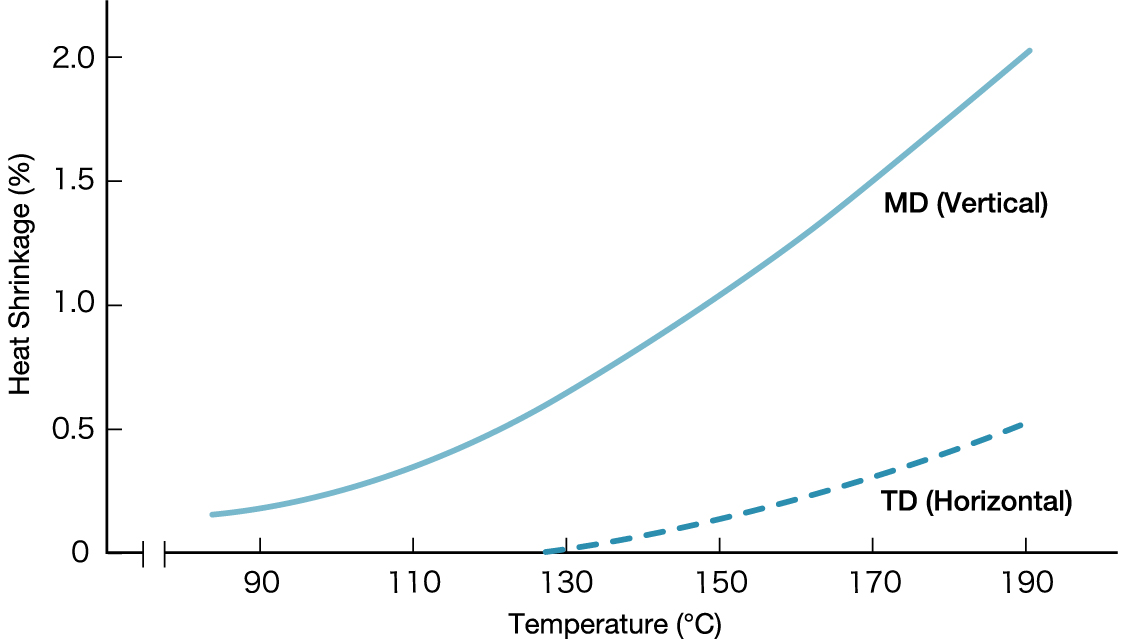
9. Water Vapor Permeability for Various Product Numbers
Table 3 shows the water vapor permeability for various Lumirror™ product numbers.
The measurement method was JIS Z 0208-73 with measurement conditions of 40°C and 90% RH.
Thickness | Water Vapor Permeability | |
---|---|---|
Product No. | μ | g / m2 / 24hr / 0.1mm |
#6 | 6 | 4.5 |
#12 | 12 | 7.5 |
#25 | 25 | 6.9 |
#38 | 38 | 5.3 |
#50 | 50 | 8.8 |
#75 | 75 | 9.2 |
#100 | 100 | 6.3 |
10. Comparison of Water Vapor Permeability with Other Films
Even among the various plastic films available, Lumirror™ has an extremely low water vapor permeability.
Table 4 shows the water vapor permeability of various plastic films for the purpose of comparison.
Lumirror™ has the same degree of permeability as polyethylene film.
The measurement method was JIS Z 0208-73 with measurement conditions of 40°C and 90% RH.
Film | Sample Thickness | Water Vapor Permeability |
---|---|---|
μ | g / m2 / 24hr / 0.1mm | |
Lumirror™ | 25 | 6.9 |
TORAYFAN™ BO * | 22 | 1.2 |
High pressure polyethylene | 30 | 5 |
Stretched polycarbonate | 25 | 35 |
Soft polyvinyl chloride | 35 | 23 |
Stretched vinyl chloride, vinylidene chloride copolymer | 30 | 1.5 |
Polyvinyl alcohol | 20 | 240 |
Cellulose triacetate | 135 | 410 |
Moisture-proof cellophane | 32 | 11 |
- Toray biaxially oriented polypropylene film
11. Comparison of Gas Permeability with Other Films
Even among the various plastic films available, Lumirror™ has an extremely low gas permeability, exhibiting excellent characteristics for food packaging, etc. Table 5 shows the oxygen, nitrogen, and carbon dioxide gas permeability of various plastic films for the purpose of comparison.
The measurement method was ASTM D 1434-72 at a measurement temperature of 25°C. For any film, the permeability is in the order of carbon dioxide, oxygen, and nitrogen, with a ratio of 3 to 5, 1, and 1/6 to 1/3.
Film | Gas Permeability | ||
---|---|---|---|
Oxygen | Nitrogen | Carbon Dioxide | |
Lumirror™ | 19 | 4.2 | 74 |
TORAYFAN™ NO *1 | 860 | 160 | 2670 |
TORAYFAN™ BO *2 | 400 | 84 | 1300 |
High pressure polyethylene | 2000 | 720 | 8900 |
Low pressure polyethylene | 520 | 180 | 2270 |
Stretched polystyrene | 1140 | 180 | 5640 |
Stretched hard polyvinyl chloride | 24 | 5.1 | 63 |
Stretched vinyl chloride, vinylidene chloride copolymer | 17 | - | 91 |
- 1 Toray unstretched polypropylene film
- 2 Toray biaxially oriented polypropylene film
12. Comparison of Organic Solvent Vapor Permeability with Other Films
Table 6 shows the organic solvent vapor permeability of Lumirror™ and various other plastic films.
The measurement method was JIS Z 0208-73 at a measurement temperature of 40°C.
Film | Organic Solvent Vapor Permeability | |||||
---|---|---|---|---|---|---|
Acetone | Ethyl Alcohol |
Toluene | Ethyl Acetone |
n–Heptane | Carbon Tetrachloride | |
Lumirror™ | 0.77 | 0.42 | 0.50 | 9.70 | 0.69 | 0.71 |
TORAYFAN™ NO *1 | 29.0 | 2.20 | 1300 | 216 | 1440 | 4540 |
TORAYFAN™ BO *2 | 1.02 | 1.02 | 661 | 85.5 | 865 | 2020 |
High pressure polyethylene | 202 | 19.1 | 1080 | 457 | 1540 | 4670 |
Stretched hard polyvinyl chloride | 4330 | 0.44 | 611 | 2220 | 0.52 | 0.27 |
Stretched vinyl chloride, vinylidene chloride copolymer |
512 | 0.39 | 358 | 493 | 0.45 | 8.1 |
- 1 Toray unstretched polypropylene film
- 2 Toray biaxially oriented polypropylene film
13. Thermal Degradation Stability
Lumirror™ features excellent thermal degradation stability.
The maximum usable temperature for Lumirror™ is generally 150°C. When planning to use it for long periods of time, 130°C or less is recommended.
Figures 7 and 8 show the changes in tensile strength and elongation of Lumirror™ after heat treatment at a typical temperature along with the heat treatment time.
The thickness of each sample used for measurement was #38 (38 μ).
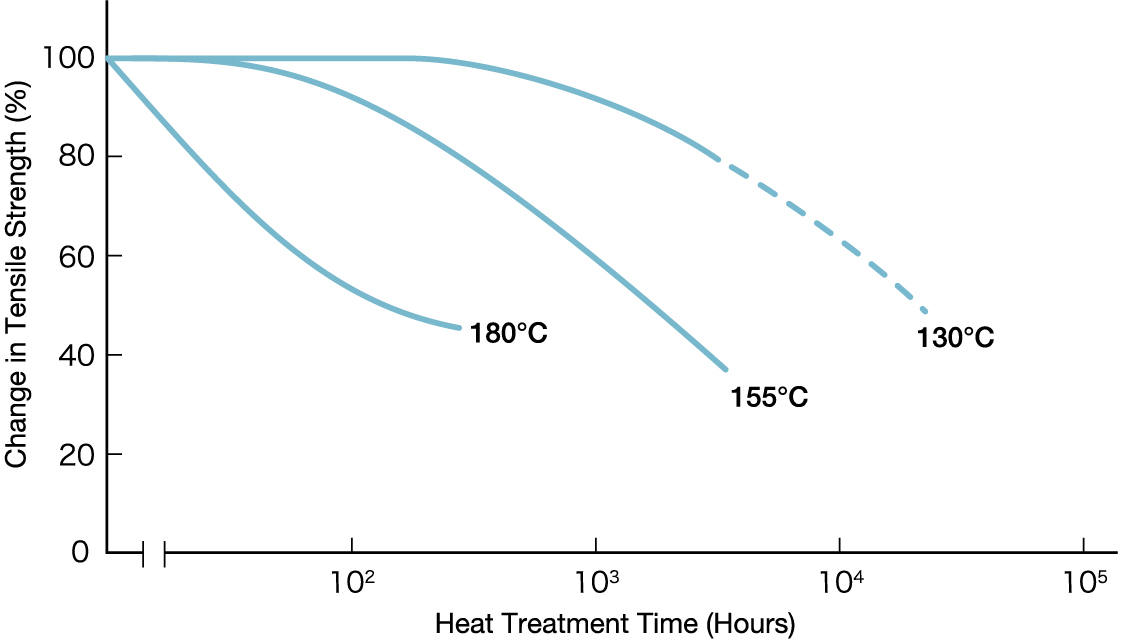
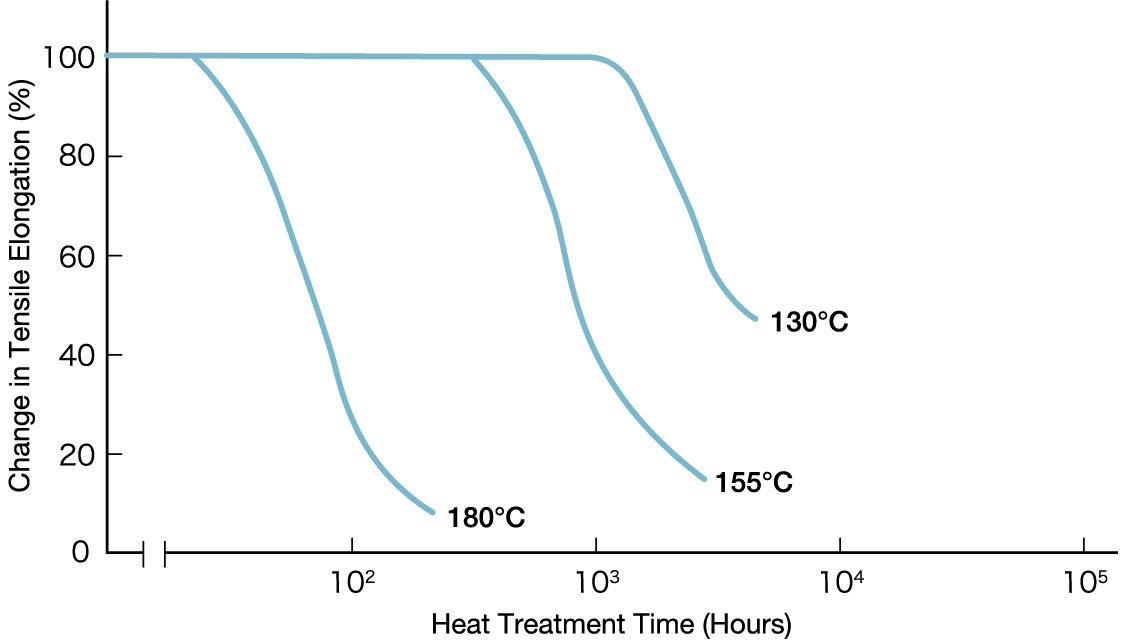
14. Heat Resistant Life
With the initial tensile strength and elongation of Lumirror™ being 100%, Figures 9 and 10 show the amount of time taken for those values to drop to 50% and 10% (representing the change in lifespan) based on temperature.
The thickness of each sample used for measurement was #50 (50 μ).
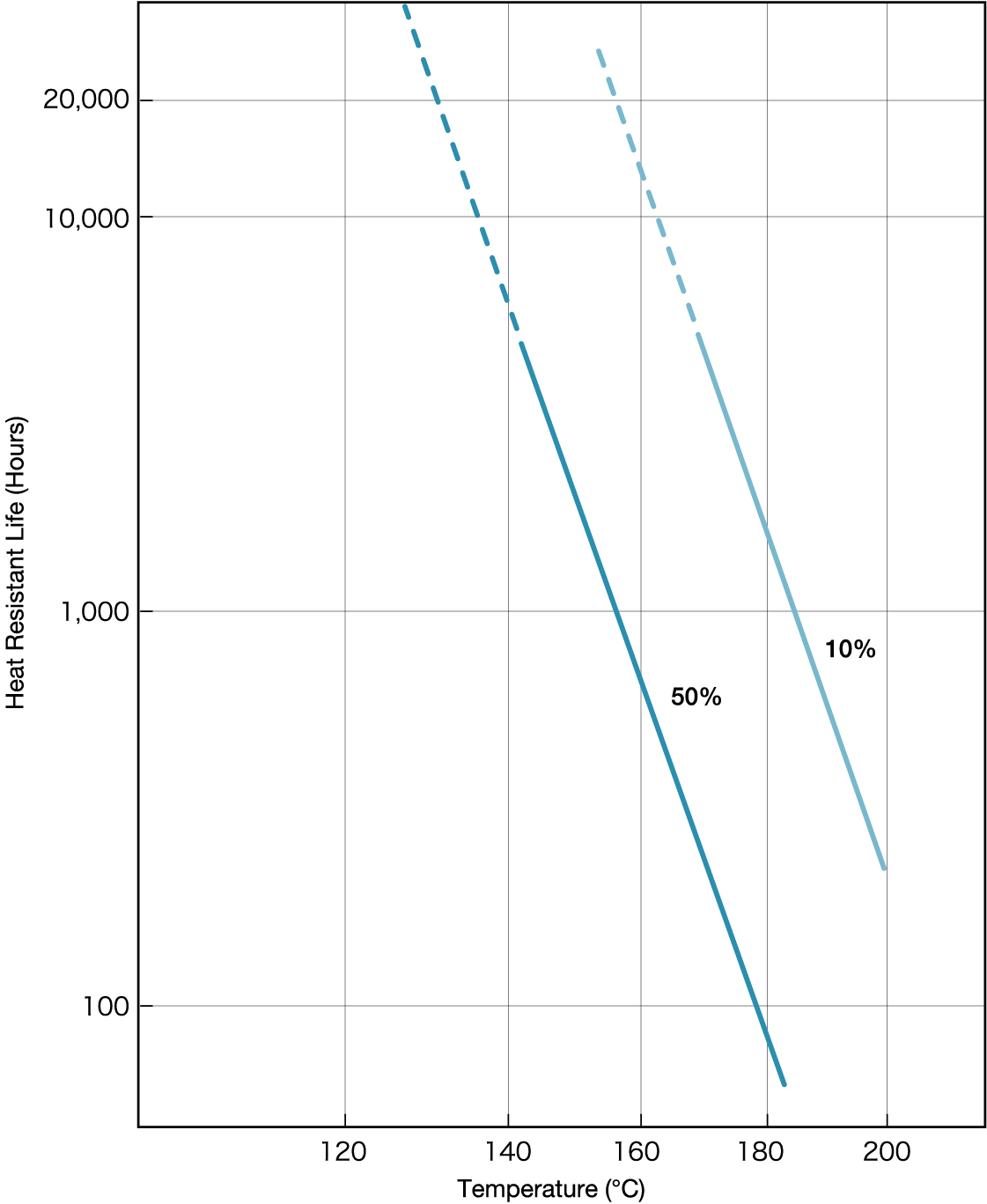
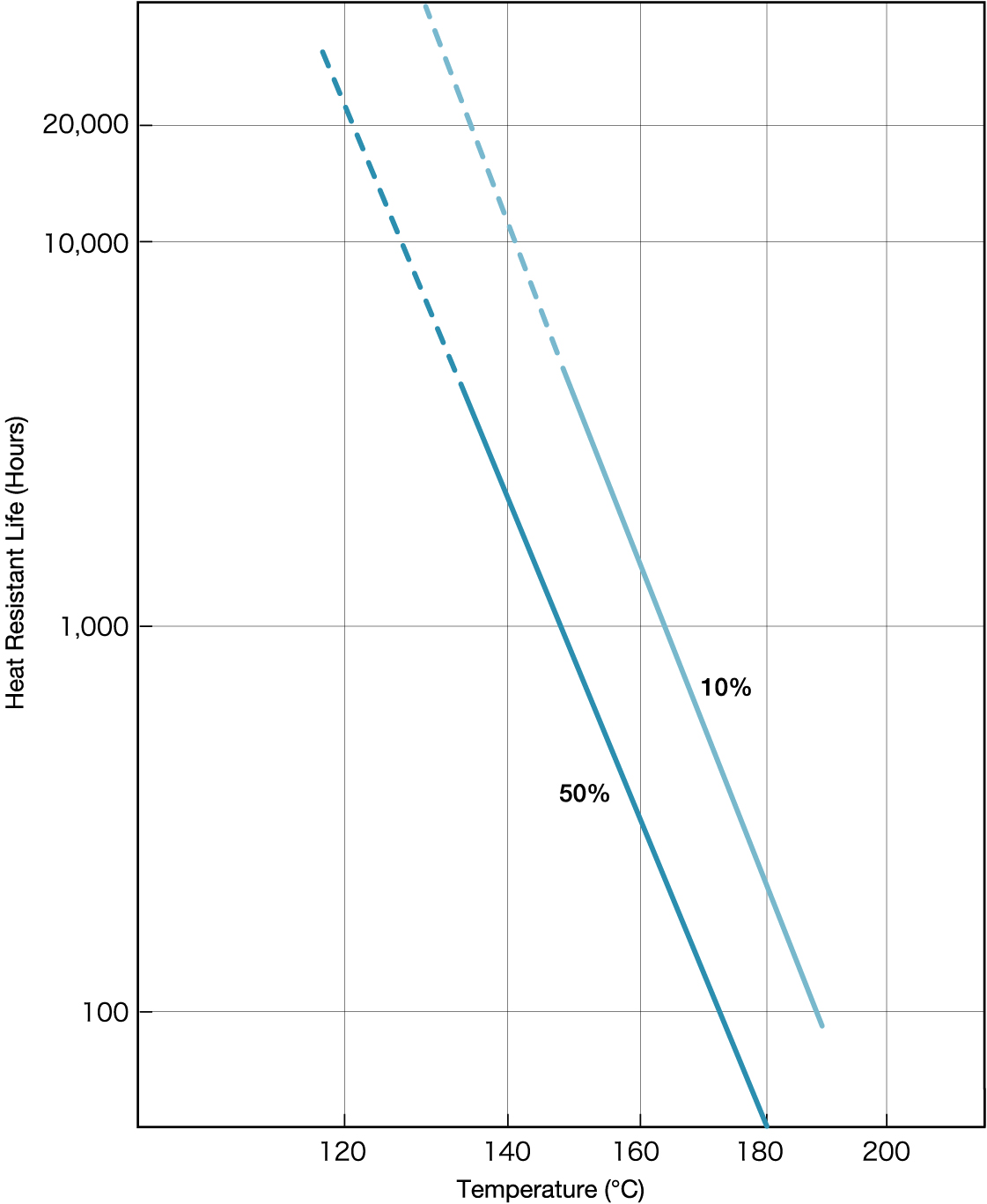